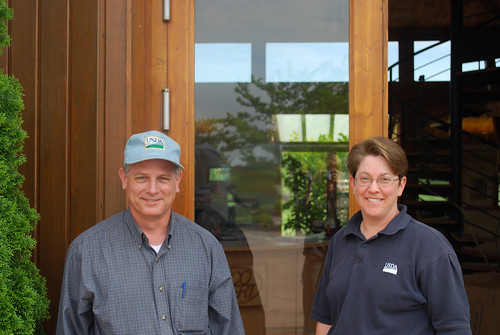
As an auditor for USDA’s Agricultural Marketing Service (AMS), I am one of a small group of highly-qualified individuals from across the country who audits companies that use our programs and services to add value to their products in the market place. One of these programs is the USDA Process Verified Program, or USDA PVP for short.
For a PVP audit, I do a significant amount of preparation before I’m even on-site, pouring over the Quality Manual the company prepared as part of their application. The Quality Manual – the starting point for any PVP – documents all of the process points, the scope of each, and the standard I am ensuring they will meet. To evaluate this effectively, I rely on my extensive training in International Organization for Standardization’s (ISO) quality management system requirements and audit principles, as well as training specific to the industry, processes, and points being audited.
When I first arrive on-site, I check-in and at an opening meeting I introduce myself to the Quality Assurance Manager and other representatives from the company. This gives us a chance to go over the finer points of the audit and quality standards or process points I’ll be verifying. If I’ve audited them before, I’ll also go over any previous non-compliance findings before I begin to make sure they’ve been addressed. These meetings are essential for establishing expectations and ensuring open communication.
Our PVP audits require intense review of records and documentation. Working through the checklist contents – for a PVP, it’s 20-30 pages long – I make sure that the checklist reflects all the points outlined in the process manual. I also review the process and production records the company has kept since the last audit. On average, I conduct between 50-75 audits per year, so I’m able to remain proficient at reviewing these types of records.
While documentation is a huge piece of my auditing, I also must visit each location that is tied to a process-verified point to see for myself and USDA that the standards that the company set for itself are being met. This means that over the course of a day or week, I might visit farms, hatcheries, feedlots, feed mills and other areas of production, as well as processing plants – all to verify different production aspects to ensure that the PVP shield truly represents the verified product that the company’s customers expect.
I also spend a great deal of time interviewing staff about their work, how they are operating within the quality control process, and ensuring that their routines and efforts are maintaining the integrity of the PVP. I speak with everyone - from farm owners to live-haul crews, receiving departments to nutritionists - to verify that staff members are trained correctly and doing their part. My agriculture background – growing up on a farm, academic training, and industry experience –help me evaluate whether these quality and process requirements are met. Depending on the process being evaluated, I may also use other training, such as that provided by the Professional Animal Auditor Certification Organization, to evaluate the company’s practices.
Once I’ve verified all of the process points, documentation, and finished my interviews, I hold an exit meeting to review my findings. These meetings are with a wide range of individuals—sometimes even the company president—but usually with management as well as the Quality Assurance Manager. To me, this level of involvement from company leadership is a testament to our clients’ commitment to ensuring the quality of products they produce.
At the exit meeting, I go over my findings. I outline any non-conformance I find and the expected course of action to correct it. I explain to them that they have 30 days to correct minor findings and 15 days for major findings, and that they will be accountable for meeting those timelines through another round of review and auditing. It’s important that they understand the severity of non-compliance, but also the path to fixing any issues.
Each audit is different and a unique experience – which I love, because it allows me to work with all facets of agriculture. The variety and complexity of these audits also require that I maintain a high level of training, not only training in ISO principles and industry practices but also certification as an American Society for Quality’s Certified Quality Auditor. I’ve been able translate the passion of my youth into in-depth knowledge of all types of agricultural production. Mostly, I like knowing that every day I’m a part of the team providing transparency and quality from farm to table.
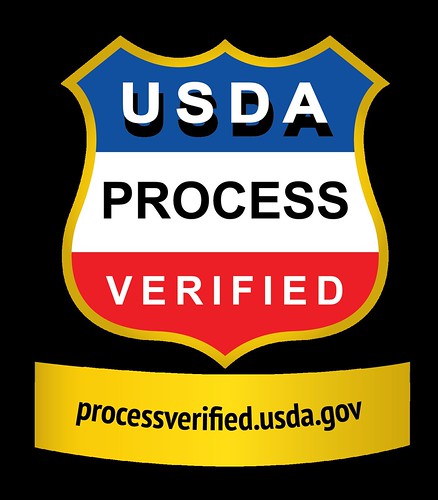